emissions and improve process control through the innovative use of Kalrez® perfluoroelastomer parts
combined with other proven packing materials. Graphite packing systems can meet fugitive emissions
requirements but restrict valve movement, leading to inconsistent process control. Polytetrafluoroethylene (PTFE) has excellent process control response characteristics but cannot contain fugitive emissions when temperature cycling is involved in conjunction with operational cycling. Kalrez® packing systems
overcome these deficiencies, as well as reducing leak rates to near-bellows performance.
Kalrez® is chemically an elastomeric PTFE derived from tetrafluoroethylene (TFE), the same base
monomer. It provides a unique combination of chemical resistance and inertness like PTFE, but with a
higher temperature service limit and no tendency to cold flow.
The chemical structure remains cross-linked and stable at high temperatures and does not move under
load or deformation. Its resiliency and memory provide improved sealing for control valve stems. Using
Kalrez® V-rings backed up with more rigid components of carbon fiber-reinforced PTFE (DuPont™
Vespel® CR-6100) has proven to be a major advancement in improving process control and reducing
leakage to less than 1 ppm, or below the plant’s background level. Kalrez® perfluoroelastomer packing
systems increase a valve’s ability to react quickly and smoothly to process changes (Figure 1). Kalrez®
KVSP™ reduces process control variability to the control system’s capability, resulting in improvements to both yield and product quality on specification.
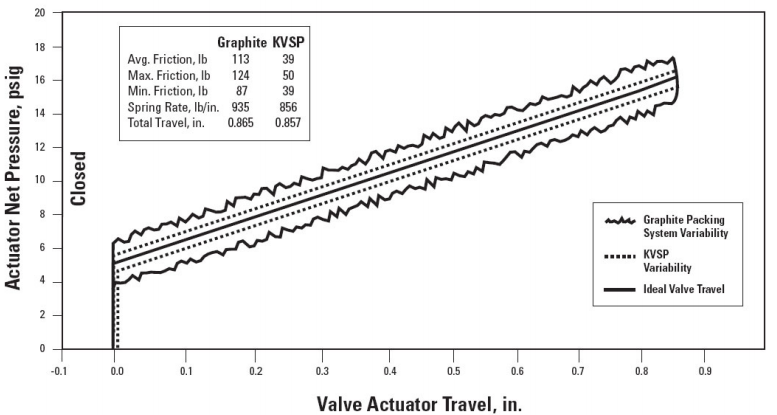
The control valve is the final control element in a process. Installing a sophisticated process control
instrumentation system capable of achieving 0.5% or better variability should improve control variability, but
many valves control to no better than 2–3%. Kalrez® KVSP™ systems move a control valve’s performance
closer to the ideal valve through low stem friction and reduced deadband. Kalrez KVSP improves the
control valve’s response closer to the optimum performance capability of the control system.
Conventional Packings PTFE square-braided and rope packings are the most commonly used packing elements for manual control valves (hand or automated on/off valves) in chemical plants, while automatic throttling control valves typically use more reliable and higher performance PTFE v-ring packing.
The inherent problem with a PTFE-type packing is that when temperature fluctuations occur in a chemical process, the material will creep and move because it is a plastic. Extensive testing has demonstrated that even live loading with a disc or coil spring will not keep fugitive emissions under 500 ppm (Figure 2). PTFE-based packing can also
cause shaft fretting or scratching from particle imbedding, while perfluoroelastomer systems repel/reject particles
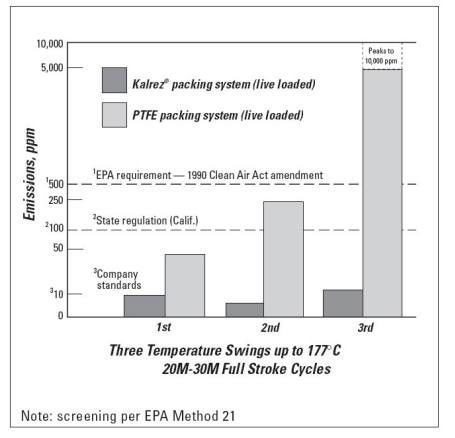
Valve Stem Packing vs. PTFE Packing Systems
Typically, with graphite, a compromise must be found between the best sealing performance and increasing the loading force.
Increased stem friction affects stem movement. The higher loading forces that are needed to seal a graphite packing at less than 500 ppm cause stiction and compromise the controlling function of a valve. This problem is virtually eliminated with perfluoroelastomer packing designs.
Compression packing systems using graphite are, by definition, microvoid structures with leak paths. The
choice has been to accept the cold flow and creep problems of PTFE-based systems and their affect on
long-term sealing performance or to use a graphite-based system with higher stem friction and an oversized
actuator and positioner. However, this still may not overcome the excessive packing stress on the stem that
leads to jerky stick-slip movement and inconsistent control.
Kalrez® KVSP™ systems use resilient Kalrez® V-ring chevron seals in combination with higher modulus
backup components. They use much lower loading forces to seal and are resilient and pliable enough to
function effectively if misalignment occurs.
Metal Bellows or Kalrez® KVSP™
The only option, until now, that could provide low leakage levels that approached 0 ppm has been metal
bellows. Because bellows have thin metal membranes, they have pressure/temperature limitations and are
subject to corrosion and cycle fatigue failures. Of course, in some extremely toxic or hazardous environments,
bellows may still be the optimum choice. When combined with Kalrez® KVSP™ as the backup packing, it
would offer the highest level of containment and safety
leakage rates provided by the metal bellows. The DuPont™ Kalrez® packing systems offer a viable option in
both absolute fugitive emission reduction levels and long-term performance.
The Kalrez® KVSP™ systems provide performance that approaches zero leakage. This was verified using a
Foxboro flame ionization leak detection device, described by the EPA in Method 21, typically used for
monitoring fugitive emission leakage of hydrocarbon-based volatile organic compounds (VOCs). The Kalrez®
KVSP™ packing systems have consistently performed to the plant’s background level, and approached the
fugitive emission performance of metal bellows technology. In addition, the Kalrez® KVSP™ systems have
been tested to over 100,000 and 250,000 cycles, and have successfully performed in the field to over 500,000
cycles.
Metal fatigue and possible catastrophic failure are the realities of using metal bellows. Metal bellows made
from special metal alloys can almost completely eliminate leakage, but the cost is inherently more expensive,
typically 5 to 7 times more than Kalrez® KVSP™.
A five-piece assembly is suggested as the optimum design or configuration for use with Kalrez® V-ring components. The suggested assembly sequence and each component size, with reference to the actual height of the packing, are noted below.
For those instances, where the optimum five-piece configuration cannot be used due to a space limitation, a three-piece assembly option is suggested. The sealing component (Kalrez® V-ring) should be maintained to provide a minimum of at least one-third of the total packing height. This ratio is the same used for the recommended five-piece assembly. Any differences in total height or the packing box length requirements can be accommodated by using a compatible metal or high modulus, chemical-resistant plastic spacer.
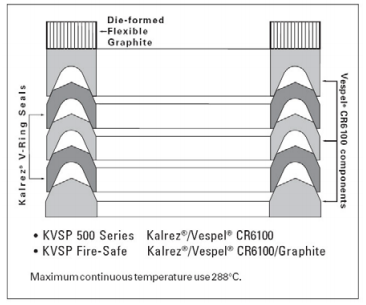
The design objective for packing should be to maximize containment while improving process control. The
surface and contact area for the elastomeric chevron sealing ring and design of the support elements are
important. Too little elastomeric sealing surface jeopardizes the system’s sealing integrity, while too much
increases the system’s friction and ability to react to process input changes.
A perfluoroelastomer packing increases the valve’s ability to react quickly to process changes, resulting in
improvements to both yield and product quality. This can be easily verified by running diagnostic tests.
Typical Control Valve Dynamics Using Kalrez® V-Rings Conventional Controlling — Dithering/Perturbations
(small stem movements) In most typical control valve applications, the Kalrez® V-ring seal components grip the stem and the elastomeric backbone absorbs the minute movements of the stem with little, if any, wear (Figure 4).
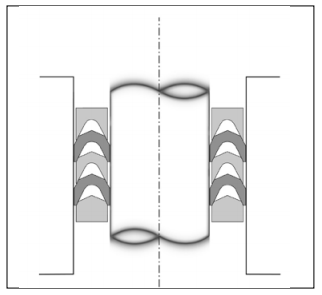
Full extension and movement are frequently used in applications that are either fully open or closed. Because the
Kalrez® packing requires less force to seal than PTFE, the packing will release and reseal with virtually no loss of sealing
and with negligible wear.
.
Stem and Packing Box Finishes
Stem and packing box finishes should be consistent with the originalequipment manufacturer (OEM) valve specifications.
Setup Procedures to take full advantage of Kalrez® KVSP™ packing and its capabilities, care must be taken during the initial installation and mechanical loading. Careful installation with Krytox® lubricant is recommended for ease of assembly and to maximize service life.
A modified setup procedure is suggested for live loading Kalrez®KVSP™ systems to ensure the correct loading force is used during the life of the packing and to avoid any over-compression of the packing . This procedure also creates open space within the spring set, allowing dynamic movement of the packing system to compensate for any volumetric changes that occur during thermal cycling.
As an alternative to the installation procedure in Figure 5, please consult the Kalrez® KVSP™ section of the Kalrez® Application Guide (KAG). This program calculates the preload spacing for the packing,
dependent on the KVSP kit selected. The KAG can be found at: www.kag.dupont.com. (Note: a number of control valve OEMs have successfully used Kalrez® KVSP™ by preloading the packing.)
The Kalrez® KVSP™ systems are designed so the components move together during service to eliminate free space within the packing system. This is part of the system’s design and will occur automatically during service without further adjustment from normal mechanical and thermal cycling.
Experience has shown that a force between 40–80 bars (600–1,200 psi) on the packing system is required from an external disc spring when set at half of its maximum compressed load rating.
Kalrez® KVSP™ systems are designed to wear differently than conventional PTFE packing. A conventional PTFE packing is, by design, forced to move and jammed-in to seal. This is how a PTFE packing functions: significant force must be applied to make it creep and move against the stem and packing box to seal. Kalrez® and the Kalrez® KVSP™ systems function and seal in an entirely different manner. They require moderate loading forces to seal. The lower loading forces required by Kalrez® translate into significantly longer service life for the Kalrez® KVSP™ systems. Packing properly
installed translates into less maintenance. Installation/Lubrication
The use of Krytox® lubricants optimizes packing life, therefore it is provided with new valve and retrofit kits. Krytox® GPL206 fluorinated grease is the only lubricant that provides chemical compatibility and thermal stability equivalent to the other fluorocarbon-based component materials used by Kalrez® KVSP™ systems. The use of
Krytox®, with the Kalrez® KVSP™ system, offers three distinct advantages:
• improves the ease of installation and decreases possible damage to the rings
• enhances the absolute fugitive emission reduction performance
• extends the life of the packing
The standard high-performance Kalrez® KVSP™ 500/Fire-Safe Series were tested to determine their
adaptability and flexibility for retrofitting into bored-out stuffing boxes in the field.
Tests verify that DuPont™ Kalrez® can successfully seal stuffing boxes bored out up to 1.00 mm (0.039 in)
over-size. They help eliminate special packing sizes and the need to re-sleeve stuffing boxes.
The Kalrez® V-rings readjust their actual size to maintain sealing by extending to wider stuffing box
dimensions while system backup elements reset in a similar manner. The Kalrez® KVSP™ systems also
adjust to small incremental stem size changes from rework or refinishing.
Kalrez® KVSP™ 500/Fire-Safe Series/DuPont™ Vespel® Components — Maximum bored-out stuffing box
dimension equals 1.00 mm (0.039 in), diametral.
Kalrez® packing systems have been used and tested to various temperature/pressure combinations
The temperature/pressure curve operational range for the Kalrez® KVSP™ systems was tested to ANSI/FCI 91-1-1994 protocol for fugitive emissions in Class 600 valves from –40 to 288 °C. It may also be used in higher pressure class
valves. Contact DuPont for recommendations.
Services Kalrez® KVSP™ systems are rated for actual continuous temperature service from –40 to 288 °C. The
actual temperature at the packing is usually lower than the process stream. A number of major OEM control valve companies have recommended Kalrez® packing systems for very high process stream temperatures, up to 427 °C. Kalrez® KVSP™ systems can also be used at low temperatures for cryogenic applications with an extended
bonnet. Live loading is necessary to seal to –40 °C.
much as 93 to 149°C with an extended bonnet. Many standard bonnet designs provide a temperature
differential and cooling effect, and can be considered for process stream temperatures in the 288 to
371°C range, based on the specific valve design
Kalrez® KVSP™ systems are available from major valve companies in three- and five-piece designs for
rising stem, rotary shaft, or manual valves. They can easily be retrofitted without costly valve
modifications. Kalrez® KVSP™ systems are manufactured at ISO 9001 facilities. Kalrez® KVSP™ has
been fitted into thousands of control and automated valves since the early 1990s. Field service reports
verify fugitive emissions still measuring to background (less than 1ppm) after five years. Kalrez® KVSP™
outperforms other packing designs in providing full containment of fugitive emissions, combined with
reduced process variability, for better yields to tighter product specifications.
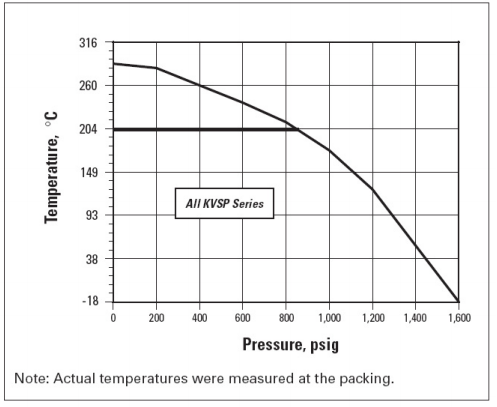
Pressure/Temperature Operating Range (–40 °C to 288 °C)
Warranty for Kalrez products
• Only applies to Dupont products distributed genuine in Vietnam.
• All Kalrez products are warranted if the machine fails due to manufacturer fault.
• For warranty and product maintenance, please contact Achilles, customer service phone number: 098 469 4884 (Ms. Duc).
• Achilles is the genuine supplier of products related to Kalrez DuPont.
• For retail/whole sale pricing, bulk ordering and product information advice please contact 098 469 4884 (Ms. Duc) via info@achilles.com.vn or the website https://achilles.com.vn/
Reviews
There are no reviews yet.